New EU Regulation On PPE
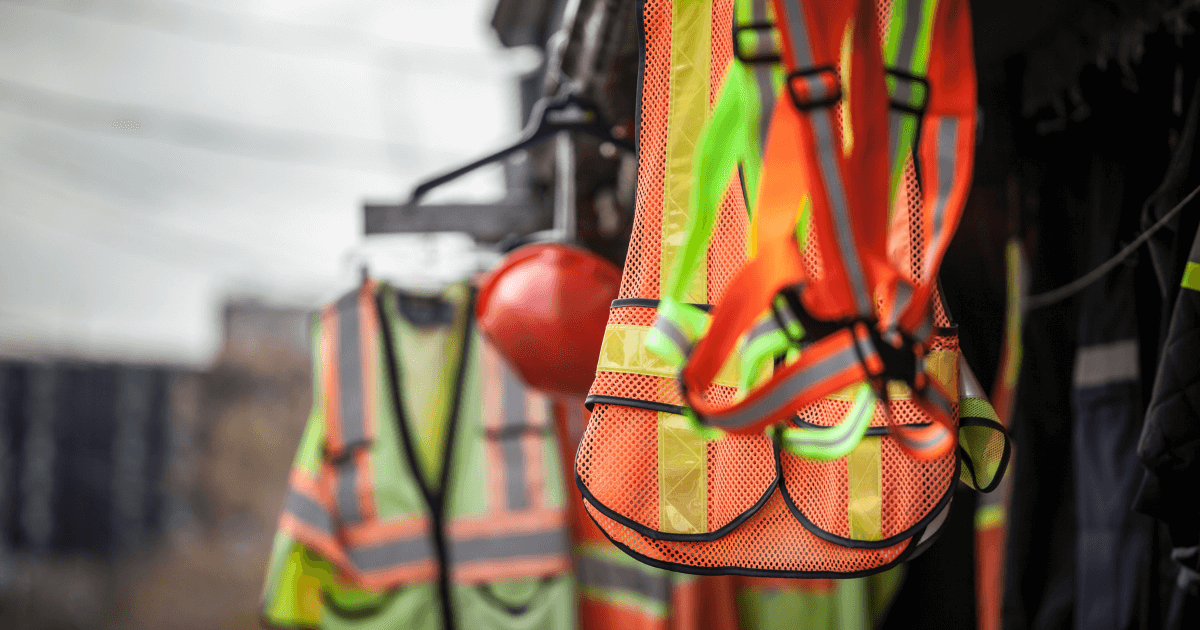
The HSE reports that around 17,000 workers are suffering from work-related noise-induced hearing loss at any stage.
When you consider those who have retired the picture is even worse, with over 70,000 people suffering from hearing loss caused by current or previous work.
Many more people face retirement unable to have a conversation in a noisy room.
The frustration with noise-induced hearing loss is that it is straightforward to prevent – don’t expose people to noise, and they won’t lose their hearing or suffer from tinnitus.
As with other hazards, reducing exposure should start by eliminating sources of noise. But once an employer has bought quieter tools and provided collective means of protection, if there is a residual risk of hearing damage, hearing protection is essential. Whilst legislation defines action and limit values, employers should remember the overall requirement that the risk of noise exposure is reduced to as low a level as is reasonably practicable.
CHAPTER 1
Laws And Regulations
Under the 2002 PPE Regulations (which implemented the earlier 1989 EU Directive) three categories of PPE were defined. Tighter controls were expected of PPE defined as “of complex design intended to protect against mortal danger or against dangers that may seriously and irreversibly harm health” with the hazard groups to which this applied listed. These hazard groups included respiratory hazards, ionising radiation, high and low-temperature environments, electrical risks and falls from height.
The current legislation which refers to the supply of personal protective equipment is The Personal Protective Equipment Regulations 2016/425, which is enforced by the Personal Protective Equipment (Enforcement) Regulations 2018. HSE is the enforcing authority for the supply of PPE that is designed for use at work.
The firstthing to note is the expansion of the highest category of PPE, such that it no longer relies on “complex design” and includes additional hazard categories such as high-pressure jets, bullet wounds, knife stabs. and harmful noise.
The secondarea of significance is that whereas the old regulations focused on requirements on manufacturers. The new regulations allocate new responsibilities to importers and distributors, who will no longer be able to rely on the claims of manufacturers for levels of hearing protection. But will need to have processes in place to demonstrate confidence in the manufacturers’ claims.
A further requirement is that examination certificates will need to be renewed at least once in five years. Hopefully, this will prompt manufacturers to keep up-to-date with the best methods of providing protection, and prompt distributors and buyers to look for the best protection available.
Hearing protection previously in the medium-risk category will have had to be certified to the higher category by April 2019. Requirements to mark hearing protection (or the packaging) with the attenuation provided (usually indicated by an SNR or single number rating) remain, but the previous requirement to show a “comfort index” has been removed.
The revised regulation concluded “experience has shown that it is not possible to measure and establish such an index.”
CHAPTER 2
What Do Employers Need To Do?
In short, the requirements for quality assurance of hearing protection will be increased, and will apply across the supply chain. However, this will only be effective if those purchasing and using hearing protection play their part. So, if your workers use hearing protection in the workplace, what do you need to do?
- If you don’t already have one, create a register of all the PPE, including hearing protection, used in your workplace. Check that ear muffs include a CE mark, and that earplugs provided have a CE marking on the packaging.
- Check who is supplying your hearing protection – are they members of the BSiF Registered Safety Suppliers scheme or a similar independently checked organisation?
- Do you have declarations of conformity and instructions for use for the hearing protection you currently use? If not, request this from your supplier or the manufacturer.
- Check that the SNR value is appropriate to the noise levels people are exposed to – it can be dangerous to over-protect hearing as it results in less compliance. Remember too that the SNR is only valid when hearing protection is worn correctly, so incorporate the instructions for use into refresher training for all workers who need to wear it.Tracking your PPE use is easier when you have a system in place, and EcoOnline includes modules to support you with this. Check out our Asset Register Software.