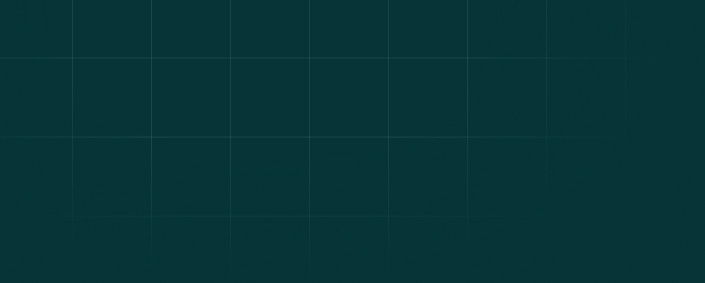
Toxin Meaning & Definition
Toxin
What is a Toxin?
A toxin is defined as a naturally occurring organic poison that’s generally produced due to the metabolic activities of an organism or living cells. Toxins are generally found in the
environment as proteins, though can also be either smaller molecules or even peptides.
The toxicity of toxins often varies greatly, with less severe toxins including a bee sting, to more severe, or potentially fatal toxins, including botulinum. These are generally different from
other chemical agents based on their origin, since toxins are generally considered to be naturally occurring.
Often created by plants or humans, the term also includes any medicines that might be poisonous in larger quantities to humans. Most toxins in the environment that harm humans are usually
released from germs, especially bacteria.
For instance, the cholera bacteria is responsible for the spread of cholera. Toxinology is the scientific study of toxins and is often viewed as a subset of toxicology. Many plants, and even
some animals, release toxins in the environment to protect themselves from predators.
Why is it Important to Learn About Toxins for Workplace Safety?
Toxic materials and toxins are commonly present in different work environments. If employees don’t know about them, they are at risk of serious harm, especially if these toxins enter their
body.
It is important for employers and for organizations to provide detailed training to employees on how to deal with toxic materials, and even look at ways to substitute toxins with less harmful
alternatives. This is obviously not as easy, but it’s highly recommended if possible.
It’s important to learn about toxins for several reasons. Some of these are discussed below.
Improve Worker Safety
Employees that work directly with toxins are obviously at an increased risk, which is why it’s so important for organizations to take appropriate measures and to detail steps on how to improve
worker safety.
This includes providing information about known toxins that workers might come in contact with, detailing any safety measures taken by the company to deal with these toxins, and information
about antidotes or steps to take in case of exposure.
Substitution
Substitution is an effective measure in reducing the risk to workers. When employers know about the toxins found in the raw materials that they purchase, they can then determine if less toxic
alternatives are available.
Wherever possible, switching out the toxins and going with a less toxic material is advised, primarily as it makes the environment safer. When thinking of substitution, employers will want to
take a look at the Material Safety Data Sheets to determine any viable substitutes.
Implementing Control Measures to Reduce Risk
When employers are aware of the toxins that workers might come in contact with, they can take measures to improve worker safety and provider a safer work environment.
For instance, to prevent exposure to toxins, companies can implement stricter control measures. From installing high-power ventilation systems to providing proper respirators to workers,
companies can implement a slew of measures to improve safety in the workplace.
Assessing Work Protocols
More importantly, when a company knows about the different types of toxins that their workers might be exposed to, they can also assess their work protocols and identify changes. For instance,
a review of the way toxins are handled, stored, used, or discarded/disposed of can be conducted as well.
Providing Safety Instructions to Workers
In the event of exposure, there should be comprehensive instructions in place on what to do. Employees should be trained and should know what antidotes to administer or what steps to take to
provide first aid and to mitigate the risk of disease or injury.
This is only possible when employers thoroughly assess the different types of toxins found in the workplace and then devise safety strategies.
Storing Toxins
Toxins or toxic materials in the workplace must be stored properly in a safe location. Ideally, the storage area should be:
- Properly ventilated and should be away from direct sunlight.
- Different toxins must be stored separately, and they should be kept away from handling or processing areas to avoid mixtures or any incidents.
- The storage area should be fire resistant and companies should use non-combustible materials.
- Ensure that cleaning stations for emergency showers or eyewash are located close by
- Proper equipment for dealing with a fire outbreak or a spill clean-up should be available.
Employers Should Record and Investigate Incidents Related to Toxin Exposure
In case an employee is exposed to toxins in the workplace due to any reason, it is important for employers to properly capture and investigate the incident.
This means making sure that they identify the reasons for the exposure, the extent of injuries or aftermath, including steps on how to prevent such incidents or accidents in the future. This
also means conducting a risk assessment again or identifying new steps to reduce risk.
Use EcoOnline’s Chemical Safety Software to Highlight Toxin Risks and Ensure Safety
EcoOnline’s Chemical Safety Software can help companies prepare records of all toxins in use in
the workplace.
The platform makes it easy for companies to provide workers with relevant information about harmful toxins and other chemicals that they might be exposed to and take appropriate steps to keep
them safe.